その他の質問について
製缶板金加工(manufacturing sheet metal)とは?
板厚3.2mm~16㎜までの中厚板を使用した製缶板金加工ならお任せ
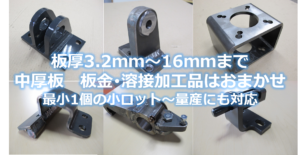
中厚板の製缶板金加工は石川県の岩本鉄工所にお任せ
製缶板金加工の定義
製缶板金加工とは、英語でmanufacturing sheet metalと訳され、実務的にはおおよそ7~8mmを超える比較的厚めの板材に対して、
切断・曲げ・溶接加工を行い製品を製作する加工法を指します。
また、切断・曲げ・溶接加工後に、さらに機械加工を行うなどして、精度あるいは平面を出すケースが実務的に多い加工法です。
板金加工が切断・曲げのみで製品を製作しようとするのに対し、製缶加工は溶接と機械加工を多用するのが特徴です。
なお、JISにおいては製缶加工の定義は、密閉された対圧力容器の製作のことを指しますが、実務的には前述の説明の通りとなります。
溶接板金加工.comの製缶板金加工の工程
溶接板金加工.comで行っている製缶板金加工に関するプロセスについて、これまでの製作実績をもとに記載をしていきます。
切断工程(ブランク工程)
製缶板金加工を行う上では、はじめの工程となる切断工程は、古くはシャーリングなどの加工機を使用して、切断加工が行われていました。
現在、溶接板金加工.comでは、トルンプ社製のレーザー加工機を使用しており、レーザーの中でもディスクレーザーという
切断能力の点で優れたレーザーを使用して、加工を行っています。例えば、下記の写真のようなヒンジ部品を加工する際にも、
切断工程が必須となります。この場合厚さ16㎜のS45C材を使用しており、製缶板金加工品としては、中厚板のクラスに属する加工品と言えます。
溶接板金加工.comでは、薄板~中厚板クラスの加工を行っています。厚板の場合には外注依頼することもありますが、基本的には、ディスクレーザー加工機を使用することで、
鉄系の板材やステンレス板、アルミ、銅板など対応領域は非常に幅広くなっています。
曲げ工程(ベンダー工程)
切断工程で、板材から必要となるサイズの板材の加工が完了した後には、曲げ工程が次工程となります。
先ほど紹介したような、ヒンジ部品を見て頂いてもわかるように、溶接板金加工.comでは中厚板の曲げ加工を中心に取り扱っています。
薄板の曲げ加工や厚板の曲げ加工はどちらも難しいとされており、
①薄板は十分な精度を出すことができない
②厚板の場合にはそもそも曲げることができない
と言ったことが問題となります。
溶接板金加工.comの場合には、”強度”が重視される建設機械を中心に行ってきた経験から、現在では、中厚板に対する板金加工を得意としており、
下記のようなベンダー機を用いて、中厚板に対する製缶板金加工を実現しています。
上記の写真もその一つで、特徴としては、複数回の曲げ加工を行っている点にあります。
曲げ加工は板材をチャッキングした後にある程度距離のある箇所に金型を押し付けることで曲げ加工が行われます。
その為、曲げ位置と板材の掴みの位置にはある一定の距離が必要であり、この距離を掴み代とも言います。
先ほどの写真のような複数回の曲げ加工品は、掴み代を充分に確保することができず、難加工形状であるとされています。
溶接板金加工.comではこのような製品に対しても、トルンプ社製のベンダー機と6軸のバックストップと角度センサーがオプションとしてついている為、
高精度の多段曲げ加工のニーズにも対応することが可能となっています。
曲げ加工品でお困りの方は、溶接板金加工.comにお問い合わせください。
溶接・組立工程
これまでの工程でみてきたように製缶板金品では必要となる板材のカットをし、曲げ加工を行います。その後、組立品が必要となった場合には、溶接工程が発生します。その為、溶接板金加工.comが得意とする製缶板金品は、多くの製品で溶接工程が含まれます。下記もこの製品の一つです。
ここでは、上記の製品を事例として、説明を行いますが、まずは溶接工程について簡単に説明をします。
溶接というのは、様々な種類が存在しており、必要となる強度や用いる材質によって溶接方法を選定します。
下記に大まかですが、当社で行うことができる溶接方法について、紹介をします。
溶接板金加工.comが提供可能な溶接方法としては、大きく2種類の方法があります。
一つ目は、ガスシールド溶接(アーク溶接)です。この溶接方法は、接合部の品質を保つと同時にアークを安定させるためにガス(シールドガス)を用います。
このシールドガスにCO2を用いるのがCO2溶接です。溶接方法の特徴としては、溶け込みが深く、母材同士の融合が強い点があげられます。
一般的には、半自動溶接とも呼ばれています。ただし、デメリットと言える部分もあり、この溶接方法を用いるとスパッタという溶接くず(溶接時に飛び散った金属の飛沫が固まったもの)が出やすく、溶接後の見た目は汚くなりがちです。この点は、最近のデジタル制御の溶接機が普及してきたことで、減ってきていると言えます。
もちろん、溶接板金加工.comが提供している溶接機はほとんどが、デジタル制御となっていており、電流・電圧の管理も徹底することで、先に上げたデメリットは抑えられる傾向にあります。
この方化にもいわゆるガスシールド溶接の方法はいくつか保有しており、シールドガスにCO²+不活性ガス(アルゴンガス等)を混合した物を使用した溶接方法である、MAG溶接やMIG溶接などにも対応が可能です。MAG溶接は、高い外観品質を要求される時に使用するもので当社では、強度が必要な場合、外観品質が必要となる場合の各々に合わせた溶接方法の提供が可能です。
2つめの方法としては、TIG溶接があります。TIG溶接といわれてもわからない・・・という方が多いかと思いますが、TIGとは、Tungsten Inert Gasの略称でタングステン-不活性ガスを用いた溶接方法で、電極にタグステンを使用している点が特徴と言えます。
TIG溶接は、高品質で美しい溶接ビード(溶接跡)が得られ、あらゆる金属の溶接に適用できるので、ステンレスやアルミ等の非鉄金属の溶接に使用することが多いです。(鉄でも使用します)
当社の場合には、鉄の使用量が多い為にS45CやSS400等で使用することが多いと言えますが、アルミやステンレスへの溶接もこちらの方法を用いることで、可能となっています。仕上り時の特徴としては、ビート表面が滑らかなため使用者の手に触れる場所に使用することが多いと言えます。
ここからは、実際に当社で加工を行った事例を用いて、溶接方法についてご説明をします。
上の写真の加工品は、”ボス”の同軸度が必要となっており、精度を”如何にだすか?”が加工に置けるポイントと言えます。一般的な製缶加工業の場合には、複数部品で構成されている銅製品をくみ上げ後に、ボス部分の同軸度だしを行います。しかし、この加工方法では、そもそも時間がかかることと、最終の仕上げ工程においては、チャッキングを行う位置の選定が困難なものとなります。
このような製品に対して、溶接板金加工.comでは、完品溶接と呼ばれる手法を用います。この加工方法は、製品を構成する全ての部品をまずは加工し、各々についてある程度の精度だしも行います。その後、溶接によりくみ上げていく手法です。この加工方法であれば、工程を短縮することができるので、加工コストも大きく抑えることが可能となります。
一般的な製缶板金加工業であれば、対応可能な溶接手法と言えますが、この完品溶接についてはどこでもできる溶接方法とは言えず、当社の特徴と言えます。
このように完品溶接を適応することで従来の加工方法よりも大幅なコストダウンが可能となりますので、気になる方はぜひともお問合せ下さい。
梱包・発送
溶接板金加工.comでは、長年、製缶板金加工業を行ってきたことから、自社での梱包作業や発送作業についても習熟しています。
自社でトラックを保有し、北陸エリアであれば、納品が可能な体制となっています。
ここまで、製缶板金加工がどのようなものであるかについて、溶接板金加工.comの製品事例を用いながら、お話をしました。
ひとえに製缶板金加工業といっても、得意な板厚や加工方法、数量、精度等企業によって様々でお客様が持つ課題を解決できる企業というのは、
各々異なります。その為、「既存の取引先で色々と小回りが利くので一括でやってもらっている」という製品の中には、別に依頼した方が良い案件が多数内包されていることがあります。
その為、ユーザーの方々からの視点としては、製缶板金加工業の場合には、得意不得意があり、特にコストがかさむ案件はサプライヤーの弱い点と言えます。
コストダウンや品質向上の視点に立った時には、まずは頼んでいる先ごとに、
「これはちょっと高いな~」
「あんまり品質が安定しないんだよな~」
という案件がありましたら、溶接板金加工.comにお任せください。